Металургичен на мед - производство на черни и цветни метали
Медни руди. Медни руди са разделени на две основни групи: сулфидна руда, чийто състав включва мед за получаване на съединение със сяра и окислени руди, в която медта е под формата на оксиди.
Мед понякога се намери в природната форма на метална мед (99.9% Cu) в смес с примесите. Въпреки това, роден медна руда е много рядко (само около 5% от световните мед депозити), а стойността им е малка в индустрията.
Сулфиди се падат около 80% от световните мед депозити. Най-честите сулфидни руди, съдържащи халкоцит (Cu2S) халкоцит, халкопирит (халкопирит) CuFeS2, борнит Cu3FeS3, ковелит CuS.
Съставът на скални руди включват кварц, двуалуминиев триокис, барит, калцит и различни силикати.
В Съветския съюз, основните находища на медни руди са в Трали, в Казахстан, в Кавказ и Узбекистан.
В момента има два начина за обработка на медна руда:
1) пирометалургична метод - директна топене руди или топене концентрат (руда обогатяване продукт);
2) хидрометалургично метод, при който рудата се обработва с разтворител, карта на медта в разтвора и не е приложимо за други компоненти на рудата; мед се утаява от разтвора чрез електролиза или химически средства.
Обработка на медни руди директен процес топене изисква много висока консумация на гориво и на потока, така че не е рентабилно.
Понастоящем по-голямата част от меден (80%), меден концентрат топене произведена (Каталог руда обогатяване), получен чрез флотация (отделяне на фини частици от руда и скални примеси, получени от различни им омокряне).
Меден концентрат се подлага на окисление печене и след изпичане прах се топи при изгаряне продукти отражателна или електрическа пещ. Понякога концентрати брикети или синтерован, след което те се стопяват в shtahtnyh пещи. В резултат на топене произвежда две несмесващи се течни продукт: в долната част, на пещ мат горната част на него - шлака, която преминава всички отпадъци и значителна част от желязото.
По този начин, въз основа процес pirometal и стомана разделяне е течни фази.
Stein представлява комплекс стопилка, съдържащ медни сулфиди и желязо (80-90%), шлака (4-5%) и други сулфиди на метали (никел, олово, цинк).
Обработка на камък, направени в преобразуватели, където чрез течна мат се продухва с въздух, при което се изгаря сяра и желязо отива в шлаката. Продуктът от тази обработка са блистер мед и конверторна шлака. Блистер мед съдържа 98.5-99.5% мед и до 1,5% на различни примеси (никел, антимон, сяра, желязо, кобалт, алуминий, кислород и други. Както и сребро и злато). Той е изложен на огън и електролитно рафиниране.
Това е общата схема на производство на мед. Сега да разгледаме с отделните операции на процеса.
На първо място медна руда се подлага на флотация обогатяване процес за отстраняване на по-голямата част от примесите и вземане на меден концентрат.
Към смления (до размер на частиците 0,05-0,5 mm) се добавя руда маслообразно вещество (минерални и растителни масла), където зърна меден сулфид, обхванати от филм масло, което допринася за тяхното последващо отделяне от скални примеси.
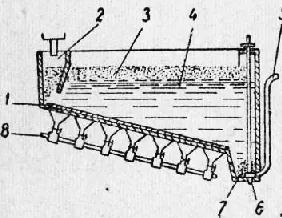
Фиг. 1. Схема на флотационни машини за обогатяване на медни руди
Понастоящем калциниране се извършва в няколко лакирани пещи с механична прегряване baniem в пещи и "кипящ слой".
Пещ с механична прегряване-baniem има формата на цилиндър с диаметър от 6-7 м и височина от 9 до 10 м. Инструменти на пещта е разделена по височина в отделения извити греди на огнеупорен (огнеупорни) тухли prichemobrazuetsya повече вътрешни палуби и един външен.
Различни пещи имат 7, 10, 12 шушулки.
Фиг. 2 е диаграма semipodovoy пещ а. В централната част на пещта преминава бавно въртящ се кух вал стомана, към която при нива на всяко отделение е обезпечен с два удара с паропрегревателя. Необходимата за процеса въздух се подава в пещта чрез централен вал прегряване-batelya и инсулти. такса за запалване е започнало, когато пещта се извършва с помощта на дюзи.
Зарядът зарежда отгоре при сушене, където се изсушава с помощта peregrebateley и постепенно доставя на захранващия отвор, през който се подава към първия, там peregrebaetsya и пада през отворите във втория преходник и т. D.
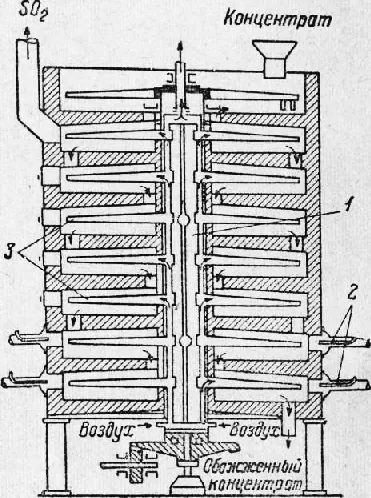
Фиг. 2. Схема многократно пещ за калциниране медна руда
Количеството на сяра се отстранява, в резултат на окисляване в зависимост от състава на заряда, неговата чистота и други причини, е от 30 до 75%.
окислителни реакции печене се появят с отделяне на голямо количество топлина, така че в повечето случаи, изпичане се извършва без разходите за гориво. Изгорелите газове съдържат 4-7% на серен диоксид (S02), който е частично окислен до S03 и се използва за производство на сярна киселина. Калциниран концентрат нарича свещ. Изпълнение с няколко огнища пещи е 250-350 тона дневно заплащане.
През последните години, нова високопроизводителна разпределени концентрати метод за печене - "кипящ слой". Фиг. "Кипящ слой" Фигура 3 показва диаграма за изпичане на пещта. На първия концентрат се подава през отвора в работното пространство на пещта. Въздухът се подава в работното пространство през отвора, въздушна камера и дюзата. контрол на налягането на въздуха да достигне позиция, която зърната на концентрата влизат в работното пространство, не попадат в огнището и да не се издигат нагоре, и се качват от въздушния поток и са в спряно състояние. Следователно, слой, подобен на кипене вискозна течност на дъното на работното пространство. Този слой се нарича "кипящ слой", "суспензия легло", "кипящ слой", и. т. р. Всяка зърно концентрат виси във въздуха и от всички страни от тях, така че окислителната настъпва много по-бързо, отколкото в няколко лакирани пещи, където зърно концентрат повечето време лежат на огнище слой и контакт с кислорода от въздуха имат само горната зърно. Калциниран концентрат (угарки) се излива от гравитацията и на прага, издаден от пещта за допълнителна обработка.
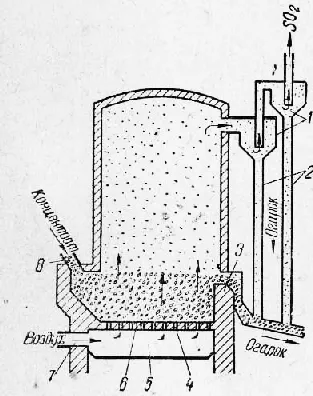
Фиг. 3. Схемата за изпичане "кипящ слой"
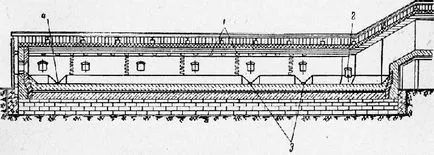
Фиг. 4. верига отражателна пещ топене щейн
За нагряване отражателни пещи, използващи нефт, газ, въглищен прах.
Зареденият смес навлиза в зоната висока температура (1400- 1500 °) и веднага се топи.
Основният процес на реакцията се определя сулфидни Cu2S, FeS и оксиди Fe203 и SiOa, съставляваща част от калцинира.
Времето, необходимо за образуване на шлака температура е около 1100 °, за да се образува матов 800-900 °, така пещ топлинна обработка е преди всичко определени условия шлака.
Непечени концентрат, което води до намаляване на производителността е около 2 пъти.
Обработка на меден камък към блистерен мед, произведен в конвертора, през който течен мат се продухва с въздух.
Най-често са хоризонтални преобразуватели (фиг. 5), монтирани върху ролки, чрез механизми конвертор накланяне за приключване на шлака и черна мед. Напълнете матова произведен през гърлото. Огнеупорната облицовка на магнезит са дюзи, през който се доставя работното пространство под налягане от 0.8-1.2 атм въздух.
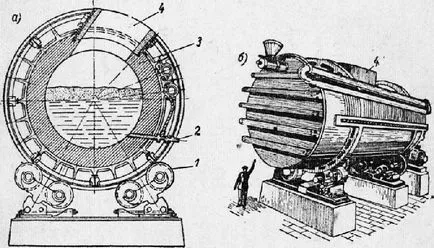
Фиг. 5. преобразувател за получаване на черна мед; разрез; 6 перспектива изглед g-
Горните реакции и тяхната последователност е показана, че желязо и сяра, имат по-голям афинитет към кислорода от мед, който окислява толкова силно през втория период само топене.
Изпълнението на съвременните конвертори от 30 до 75 тона на черна мед за всяка транзакция.
по време на обработката Bessemer мат медни средните стойности на 10-12 часа. но може да достигне до два дни, поради присъствието в камък голямо количество сяра и желязо (до 80% от теглото), които по време на процеса Bessemer трябва да бъде окислен.
Процесът се дължи на топлината на окисление на сяра и желязо. Тази топлина поддържа температурата в конвертор в първия период в границата 1250-1350 °,
Fire рафиниране на черна мед, произведен за отстраняване на различни примеси, които се влошават механичните свойства и електрическата проводимост на мед. Процесът протича на огън рафиниране огнище отражателна пещ (топилна пещ, подобен на мат), където блистерната мед се окислява с въздух, който се издухва през тръба желязо в течната мед. Получените в същото меден оксид като мед окислява примеси в поп шлаката. Впоследствие деоксидирана мед (възстановяване на излишък от меден оксид) произвеждат овъглени дървени стълбове при разбъркване ваната (което спомага за освобождаването на разтворени газове от ваната) и въглен са бомбардирани върху повърхността на вана.
Пещта се зарежда с твърд или течен превръщане мед. Капацитет модерен рафиниране пещ достига 250-400 тона мед.
Продължителност на рафиниране зарежда в пещта на твърдо вещество мед е 16-26 часа. и при зареждане течна мед - 10-14 часа.
Електролитно рафиниране на мед произведени, за да получи най-чиста мед (99.9% Си и по-висока) и свързаната с възстановяването на злато и сребро, които почти винаги се съдържат в медта блистерната и рафиниране на изпичане напълно остане в мед. В момента, електролитното рафиниране е подложена на около 95% от всички произведени в страната ни мед.
За електролитното рафиниране на мед след пожар рафиниране хвърлен в анодни плочи. Последно поставя върху специални "суспензии в електролитна вана пълна с вода. физиологичен разтвор на меден сулфат и сярна киселина (около 200 г / л). Между анодните плочи в ваната са тънки (0.6-0.7 mm) лист от чиста мед - катоди за електролитно отлагане на мед върху тях. Когато ваната в електрическа верига меден анод разтваря в електролита и отлага върху катодите и благороден
и някои други метали (например, селен, телур) попадат в шлаката (утайка на дъното на банята). Плътността на тока прилага за електролитно рафиниране, и 100-200 на 1 м2 катодната повърхност. баня напрежение от 0.3-0.35 инча Среден добив утайка е 0.2-0.5% от теглото на анодите. Утайката от електролизата на мед се събира и се подлага на допълнителна обработка за възстановяване на злато, сребро и други ценни метали.
Продължителността на разтварянето на аноди средните за 20-30 дни. Енергийна консумация на тон на медни катоди 200-300 кВтч.
Планът за седемгодишната (1959-1965 GG.), Изискан производство на мед се увеличава с 1,9 пъти.