водород атака
Корозия и защита от корозия
Водородът корозия може да придружава много технологични процеси, които се извършват при повишени температури между 200 ° С и налягане от 300 МРа в среди, съдържащи водород. Тези условия съответстват на такива процеси като хидрогениране на въглища и нефт, амоняк и синтез метанол, и др.
Има два вида на увреждане на метал с водород - водород трошливост и водород корозия. Често тези явления се наслагват един върху друг. Ако амоняк газ е налице, то може да се появи азотиране метал.
При контакт с азот смес от водород с метал при повишени температури и налягания, молекулярен водород се дисоциират върху метална повърхност. Получената атомен водород дифундира в металната решетка и се разтваря в него. Когато температурата падне поради намаляване на разтворимостта на водород тенденция да премине в газообразно състояние вътре в метала. В този случай, на метала с високо напрежение, което води до необратимо нестабилност.
Водородът корозия е резултат на химическо взаимодействие на водород с карбид стомана компонент. Външно проява корозия водород е силно намаляване на силата на стомана без съществено увреждане повърхност. Появата на корозия на водород е свързан с няколко явления:
проникване на водород в стомана продукта и образуването на крехка желязо твърд разтвор от водород;
Както се вижда от експериментални данни появата на водород корозия на външни признаци предхожда инкубационен период, който, в зависимост от условията може да продължи до 1000 часа.
При температури над 300 ° С върху металната повърхност паралелно с процеса на реакцията на decarburization протича водород хемисорбция-TION и разпадане в атоми. Диаметър водороден атом е 0.1 пМ, и има висока мобилност.
Тя не излезе на повърхността и във вътрешността на метала. Разработва високо вътрешно налягане. Pa метална повърхност блистери и се появяват пукнатини.
Термодинамичните изчисления показват, че при температури от 300-600 ° С и повишено налягане на водорода се появява почти пълно разлагане на цементит.
Тя е обратима и се предлага с намаление на обема. Следователно повишаването на налягането измества равновесието на реакцията надясно и намалява граница на температурата на реакцията. В нефтохимическата промишленост, работещи в редуцираща атмосфера при налягане до 50 тРа работна температура е ограничен до 200 ° С
скорост водород корозия е до голяма степен зависи от дълбочината на decarburization на стоманата. Този процес се влияе от налягането на водорода, температурата и т.н. (Фиг. 6.9).
Типични материали на конструкцията за намаляване среда и 20 са стомана ZOHMA. Те се работи при температура от 300 ° С За продукти, които работят при по-високи температури, е въведена в металните добавките. Елементите, използвани като добавки, които увеличават устойчивостта на обезвъглеродяват стомана, като хром, молибден, ванадий. Хром допълнително предотвратява проникването на водород в метала.
Както се вижда от фиг. 6.10, проникване на водород в стомана хром зависи от температурата на газ и съдържание на хром в метала.
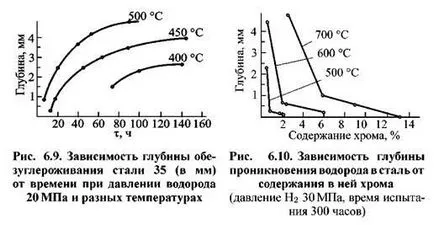
Когато съдържанието на железни сплави 6% хром химическа устойчивост на сплавта при 600 ° С и налягане от 30 МРа е достатъчно високо.
която е включена във формата на включвания на много медни сплави:
Получената водна пара създаден в метал високо налягане, което може да доведе до напукване и загуба на пластичност
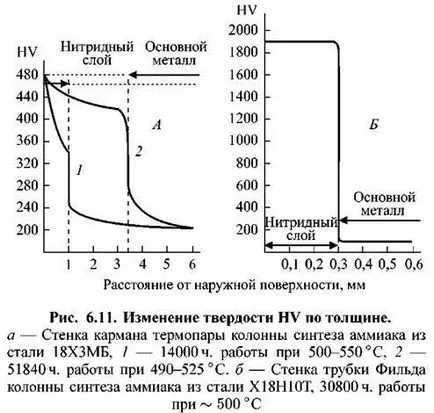
не повече от 0.01% водород корозионни явления се наблюдават.
Условията за синтез на амоняк на азот-водород-амоняк смес да станат по-опасни от чист водород. В този случай, азотиране може да се случи в допълнение към всички видове водород корозия на стомана.
Работните условия на колоните за синтез на амоняк е не само образуването на амоняк, но частично дисоциират на металната повърхност с образуването на атомен азот. Последният реагира с атомите желязо или легиращи елементи, образуващи нитриди. В резултат на стоманената повърхност е наситен с азот и става чуплив.
С увеличаване на съдържанието на хром в стомани степен от водород и излагане амоняк намалява. Когато съдържанието на хром над 11% от повърхността на стомана, за да се образува твърдо вещество и плътен нитрид слой, който предотвратява разпространението на азот в метала. Това се потвърждава от данните на фиг. 6.10 и 6.11.
На стомана 18HZMV нитрид слой дълбочина от 3-4 mm и плътност е 2 пъти по-голяма от основния метал. В стоманени части XI8N10T нитрид дълбочина слой от 0.3 mm и плътност 10 пъти по-висока от тази на основния метал.